What Is Supply Chain Risk Management?
Find out more about the functionality of SCRM and how critical it is for companies to implement SCRM strategies to avoid damaging disruptions, delays, and more.
Supply Chain Risk Management, or SCRM, is a systematic approach to managing supply chain risk that identifies susceptibilities, vulnerabilities, and threats throughout the supply chain and develops mitigation strategies to combat those threats, whether presented by the supplier, the supplier's product, and its subcomponents, or the supply chain itself.
That’s a bit long-winded. Let’s break it down a little further.
Defining Supply Chain
We’ll start with the first component of SCRM, which is the supply chain itself. A supply chain is a network that connects a firm and its suppliers to manufacture and deliver a certain product to the end-user.
This network consists of many activities, individuals, entities, information, and resources. The supply chain also symbolizes the stages involved in getting a product or service from its initial condition to the client.
Who Is a Part of the Supply Chain?
A supply chain is a sequence of processes that must be followed to provide a product or service to a consumer. Moving and processing raw resources into completed goods, transporting those items, and distributing them to final users are among the procedures.
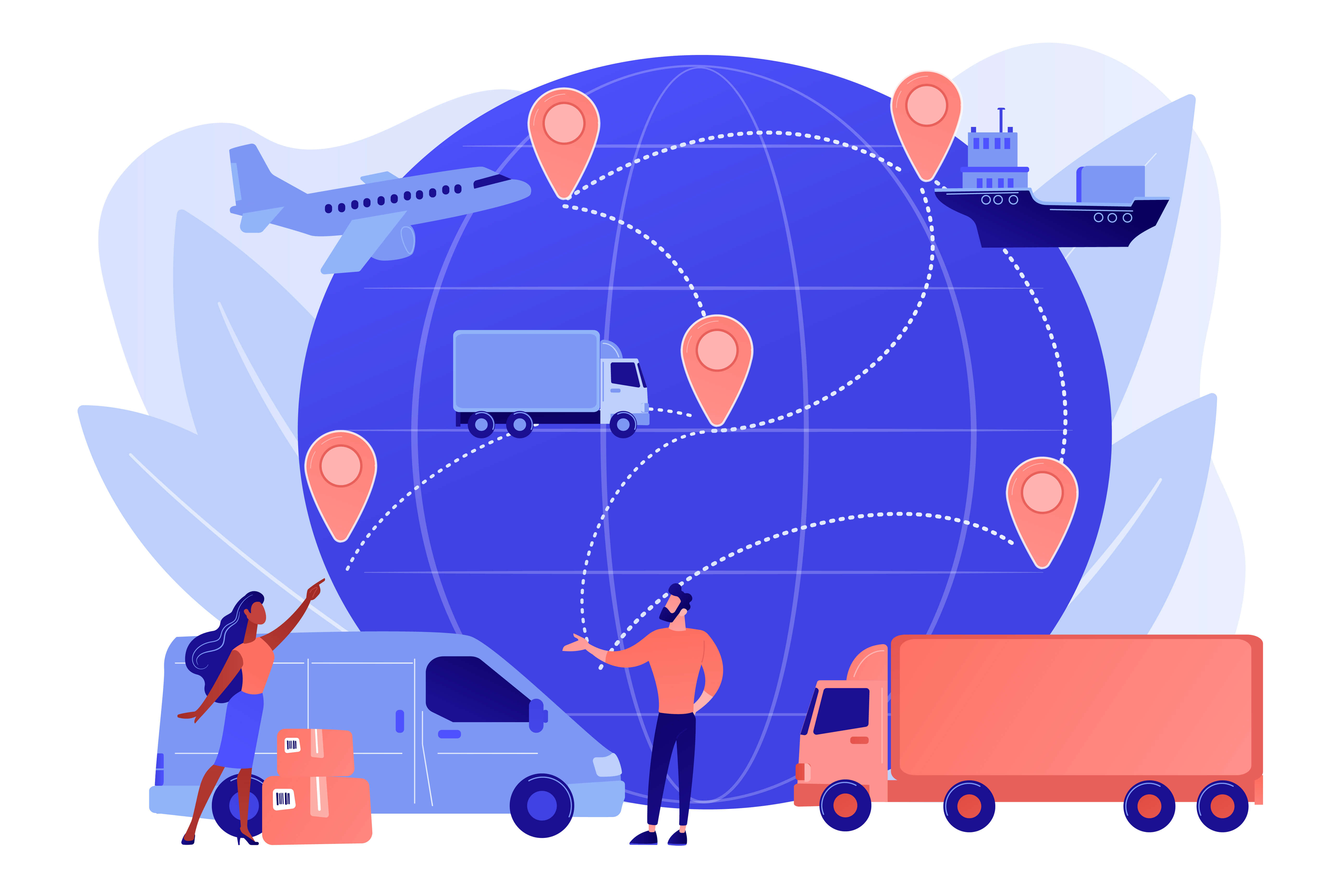
Producers, suppliers, warehouses, transportation firms, distribution hubs, and retailers are all part of the supply chain.
What Are the Elements of a Supply Chain?
A supply chain's elements encompass all of the functions that begin with receiving an order and end with satisfying the customer's request. Product development, marketing, operations, distribution networks, financing, and customer support are examples of these tasks.
SCRM’s Role in Supply Chains
Supply Chain Risk Management is a critical component of the business process. There are several links in SCRM that require knowledge and expertise.
When SCRM is done correctly, it may reduce a company's total expenses while increasing profitability. If one link fails, it can hurt the remainder of the chain and be costly.
It’s no wonder that 81% of companies focused on supply chain planning in 2021.
Risk Management
The next component of SCRM to break down is “risk management.” Countless risks pose a threat to supply chains everywhere, but here are a few of the prevalent and specific ones:
- Extreme weather events/disruptions
- Counterfeit production
- Cyberattacks
- Geopolitical risks such as human rights violations, protests, and more.
The goal of SCRM is to properly manage and mitigate the potential impact of disruptive risks like the ones written above. Severe weather events and other risks can lead to extreme lapses in a company’s supply chain, and can potentially lead to the following:
- Loss of data
- Loss of profits
- Exposure to lawsuits
- Brand and reputational damage
- and more
The primary difficulty in managing risks is that suppliers offer varying amounts of transparency. Some suppliers are open books about their policies and practices. Yet most suppliers are not so reliable.
Supplier visibility is one of the leading challenges for businesses looking to improve their SCRM capabilities. Tools like Z2Data’s Supply Chain Watch offer greater supplier visibility for companies looking to improve visibility within their supply chain by conducting part-to-site mapping and more.
A Deeper Look at Supply Chain Risks
When conducting a high-level analysis of supply chain risks, it’s necessary to identify the seven key areas of risk:
- Disruption
- Forecast
- Delay
- Inventory
- Technology/component
- Supplier
- And Site
Let’s define and analyze each of the seven risks listed above.
Disruption Risk
Disruptions are, by definition, external and macro-level events affecting a supply chain. Natural disasters, geopolitical events, pandemics — these are just a few examples of macro-level event types that potentially disrupt supply chains.
While disruptive events do not occur often, they do cause significant delays in business continuity. In March of 2000, for example, a lightning strike caused a factory fire at Royal Philips Electronics (a Nokia manufacturer) and damaged millions of microchips.
Yet Nokia's production suffered very little due to its multiple-supplier strategy and responsiveness. However, another mobile phone customer of the Philips plant, Ericsson, experienced significant disruption due to having no other source for microchips.
This example highlights the importance of an SCRM system that enables companies to multisource their products and not become too reliant on a single supplier/manufacturer.
Z2Data’s Supply Chain Watch enables visibility into available alternative parts sourced from various suppliers and also maps out your supply chain down to a sub-tier level.
Even if a disruption were to happen at a sub-tier supplier (that you may not even know about) you would be notified and assisted in strategically initiating a move to alternative manufacturing sites, suppliers, or parts.
Forecast Risk
Forecasting enables companies to gauge the market accurately and assess their supply chain relative to market needs. Without dedicated supply chain forecasting, companies run the risk of improperly projecting demand and either over or under-supplying the market. Improper forecasting of internal product lifecycles also plays a role in forecast risks.
.jpeg)
Any small change in demand can result in a large change in supply. If you do not have a flexible supply chain (from a manufacturing standpoint, this means you can secure a large amount of supply very quickly. i.e. redundant suppliers) or very accurate demand forecasts, then your supply is susceptible to the "bullwhip effect." The bullwhip effect occurs when consumer demand appears stable, but demand variability becomes more amplified as you move further up the supply chain.
A potential solution to forecast risks is to increase manufacturing, order fulfillment, and product lifecycle responsiveness to reduce the risk of inaccurate forecasts.
Delay Risk
Delays are disruptive, logistical events that create an inability to deliver on time. Delays stem from both external and internal sources. Port closures and airport shutdowns are examples of delays external to a supplier's control while overselling to the point where demand cannot be met is an example of an internal delay.
If a company regularly experiences issues with delays, it may potentially lose customers due to an inability to meet customer demand.
Access to alternative parts and suppliers reduces the risk of logistical delays. Stocking inventory in a way that keeps costs low, aggregates demand (to serve multiple markets), and increases responsiveness (produce products faster.) also aid in avoiding the impactful risks of delays.
Inventory Risk
Inventory risk is defined by multiple factors: rate of obsolescence, demand and supply uncertainty, optimal on-hand inventory, and the number of supplier sites used around the world. A company's inventory risk can be divided into two categories:
- End product inventory risk — inventory risk factors relative to a company's end product
- Component inventory risk — inventory risk factors relative to myriad components used to create end products
Inability to maintain a balanced inventory strategy results in either incurring too much cost due to overstocking of inventory or not having enough on-hand inventory to meet changes in demand or supply.
Increased responsiveness and flexibility can reduce the risk of inventory and delay risks. Companies can also minimize inventory risk by working with a highly responsive supplier, especially for high-value, short-life-cycle products.
Excess capacity can also lower the amount of inventory required. For example, by running plants at 80% utilization, Toyota can handle demand variation without having to hold inventory.
Technology & Component Risk
Technology and component risk can be divided into 4 categories:
- Obsolescence: a company's risk for components becoming obsolete
- Compliance: a company's ability to comply with RoHS, REACH, Prop 65, etc.
- Need for multi-sourcing: how many parts present a high risk for scarcity and need options for multi-sourcing?
- Pricing/cost: pricing and cost trends for components and what a company should do if they're overpaying for parts.
If a company is not accounting for tech/component risks, then it becomes susceptible to redesigns.
Lifecycle forecasts, alternative parts, PDNs, and compliance alerts all increase a company's responsiveness to technology and component risks. Greater commodity trend visibility allows for advantages in component negotiations and purchases.
Supplier Risk
Let’s state the obvious: it’s important to know who you’re working with. There are five key areas you should investigate when surveying suppliers:
- Financials: Is the supplier financially sound? Or, do you measure the financial risk of a supplier?
- Geographic: Is the supplier located in a politically stable location? Which countries do you think are most important for your supply chain?
- Reputation: Does the supplier have a sound reputation, or do they have a history of compliance/labor violations?
- Market consolidation: How consolidated is the supplier in their respective market(s)?
- Relationships: What is the supplier's current clientele? Does one customer represent a significant portion of their earnings?
Understanding how prone your supplier is to disruptions such as geopolitical events, financial events, political events, etc., allows you to increase flexibility and strategy within the supply chain.
Greater visibility of a supplier's financials, relationships, and reputation allows you to understand the supplier's risk. Additionally, understanding your supplier's supply chain allows for greater responsiveness during supplier incidents.
Site Risk
Site risk relates to a company’s potential supply chain risks regarding the locations of its suppliers. There are two key areas of site risk:
- Location-specific geographic risk: Some supplier sites run the risk of increased disruptions depending on proximity to areas with increased geopolitical or natural disaster events.
- Multi-sourcing site risk: Sites with increased risk of disruptions create a need for alternative, contingency sites.
Disruptions occur all over the globe, however, they do occur less often in certain areas. Knowing which suppliers are less prone to disruptions allows you to better consolidate your supply chain.
Mapping out the manufacturing sites that your suppliers and sub-tier suppliers are using is crucial to mitigating site risk. For example, the AKM fab factory fire could have affected your parts because one of your suppliers may source their parts from AKM. First, you have to understand your supplier sites, then you have to understand the supplier sites' risk for factory fires, natural disasters, political unrest, etc.